Vacuum insulation panels: Edge effects
The edges of a VIP represent a not inconsiderable thermal bridge. The aluminium layer in the envelope foil therefore has to be made as thin as possible (preferably < 100 nm) to keep the heat flow at a minimum. The picture below represents the isotherms and the direction of heat flow in a panel. The more distorted the isotherms are at the edges, the greater the thermal bridge.
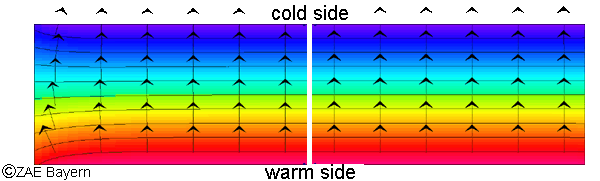
Cross-section of two vacuum insulation panels. The panel on the left is wrapped in a foil with an aluminium thickness of 8 µm and the aluminium thickness of the foil on the right is 80 nm. The orientation of the heat flow is depicted with arrows, the isotherms with lines and the temperature distribution with colours. A thermal bridge can clearly be seen in the panel on the left.
The foils currently in use have an aluminium layer with a thickness of between
50 nm (metallized plastic films) and 10 µm (metal foils).
The aluminium layer is necessary to prevent gas penetration.
Aluminium is preferable due to its tensile strength, availability and low
cost, yet it has a high thermal conductivity of 200 W/(m·K), meaning
considerable heat transfer can occur - depending on the thickness of the aluminium
layer - which by far exceeds the heat transfer through the centre of the panel.
The heat transfer via the plastic part of the foil is negligible in comparison
since the thermal conductivity of the plastic is a thousand times less than
that of aluminium.
VIP manufacturers generally only state the heat transfer value for the centre
of the VIP. However, the effective heat transfer coefficient (U-value) depends
on the size of the panel and how the VIPs are installed. The influence of
the size of VIPs and the type of envelope used was calculated for a wall.
A 17.5 cm thick sand-lime brick wall was insulated with 3 cm thick
VIPs plus 3 cm thick polystyrene. An infinitely large panel thus constructed
would have a U-value of 0.14 W/(m²K). The graph shows the effective
U-value of the wall in the case of two different foils with aluminium layers
of 8 µm and 80 nm, respectively, as well as a stainless steel
envelope of 200 µm at the edges, dependent on the length of the
square panel in each case. The effective U-value of a 0.5 x 0.5 m²
VIP, for example, is about three times larger than the U-value for an infinitely
large VIP with an 8 µm aluminium foil.
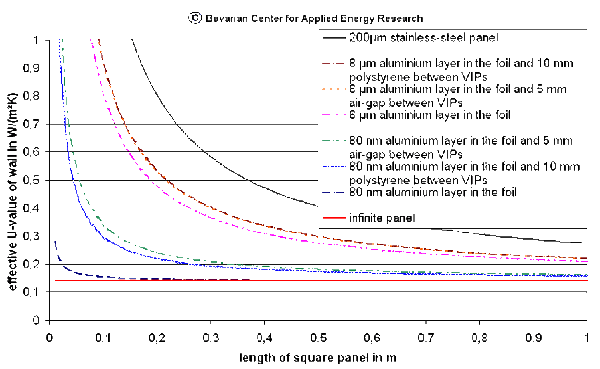
Effective heat transfer coefficient U depending on the length of the square panel for different foils and joints. Wall structure: 17.5 cm sand-lime brick wall insulated with 3 cm thick VIPs and 3 cm polystryrene.
The heat transfer via the edges can therefore considerably increase the total heat flow through the panel. This means that large panels with favourable edge/surface ratios have a smaller total thermal transmittance than smaller panels.